Sticker shock knocks the wind out of most people when they get a quote to replace a boiler. You’ll hear numbers tossed around that feel closer to buying a used car than swapping out a noisy metal box in your cupboard. Ever wonder what could possibly drive those costs up? Here’s the truth hiding behind the invoice: the price doesn’t just cover a shiny new machine. It’s a cocktail of technical know-how, regulations, sneaky parts costs, and even global economic headaches. Let’s rip apart the bill and figure out what's really jacking up the price of a new boiler.
Breaking Down the Real Cost of Boiler Replacement
First off, it’s not just about picking a boiler off the shelf and plugging it in. There’s a load of pre-work that bites into your budget. Home surveys, old system checks, and sometimes even structural assessments are needed before anyone lifts a wrench. Here’s a little-known fact: most installers in New Zealand, and especially in places with older housing stock like Dunedin, have to confirm your pipes, walls, and vents can even handle a modern boiler. If your house is a bit on the quirky side (think century-old villas), expect extra checks. That’s time and expertise, both billed at a premium.
Labour is the big elephant at this party. Skilled gasfitters and registered plumbers with the right tickets aren’t cheap, and there’s a good reason for it: muck up the job, and you’re looking at anything from leaks to real safety issues. A legit, experienced install team brings peace of mind, but it’s reflected in the bottom line. You’re not paying for brute muscle—you’re shelling out for years of training, licensing, and the kind of problem-solving that only comes after installing hundreds of systems.
Let's talk about the boiler itself. The price tag on modern units can be double what you’d pay a decade ago. Energy efficiency standards have leapt forward, and so have the materials: stainless steel heat exchangers, smart controls, and safety systems are all packed in, and they come at a cost. Plus, nearly every decent boiler these days is imported, and if you’ve checked the headlines, you know the global supply chain still feels like a game of Jenga after COVID and the Ukraine crisis. Shipping delays, parts shortages, and currency swings all find their way into your bill.
Here's a quick look at what typically makes up the total boiler replacement cost:
Cost Component | Estimated Percentage of Total |
---|---|
Boiler Unit | 35% |
Labour & Expertise | 40% |
Parts (Pipes, Valves, Fittings) | 10% |
Regulatory/ Compliance Checks | 10% |
Waste Removal/Old Boiler Disposal | 5% |
That’s the breakdown most Dunedin homeowners see, but every job is different. Swapping like-for-like on a modern house usually means less hassle and money. Upgrading a clunky old gravity system with ancient copper pipes tends to pile on the extras: venting upgrades, new wiring, and even upgraded gas supplies. Don’t forget the dreaded “unforeseen issue”—you know, the bit of 1960s wiring or the cracked flue hidden in your walls. Cha-ching.
The Role of Regulations and Safety Checks
Don’t underestimate what red tape can do to a project bill. New Zealand’s building codes are strict, but for good reason. Boilers rely on combustible fuels and pressurised water—get it wrong, and you’ve got a recipe for fires, leaks, or worse. Every installer must follow the Gas (Safety and Measurement) Regulations 2010 and the NZ Building Code. That means paperwork, inspections, and sometimes third-party signoffs. More steps, more costs.
If the installer discovers your home’s gas line doesn’t meet the new safety standards or your chimney’s not up to venting a condensing boiler, expect extra work. Upgrading vents, reinforcing floors, or even cutting new flues through brick all land on your invoice. These aren’t just for show—they’re legal requirements, and ignoring them is both risky and illegal. The upside is safety. The downside is, well, your wallet takes a hit. Compliance checks alone can add several hundred dollars, depending on your council’s requirements and whether you need gas certificates or council sign-off.
Tip for homeowners: don’t try shortcuts here. The penalties for shoddy or unlicensed boiler work in New Zealand are hefty. Plus, insurance companies are quick to void cover for dodgy jobs. It pays to ask your installer for all their paperwork upfront so you’re not sweating when it comes time to sell the house.
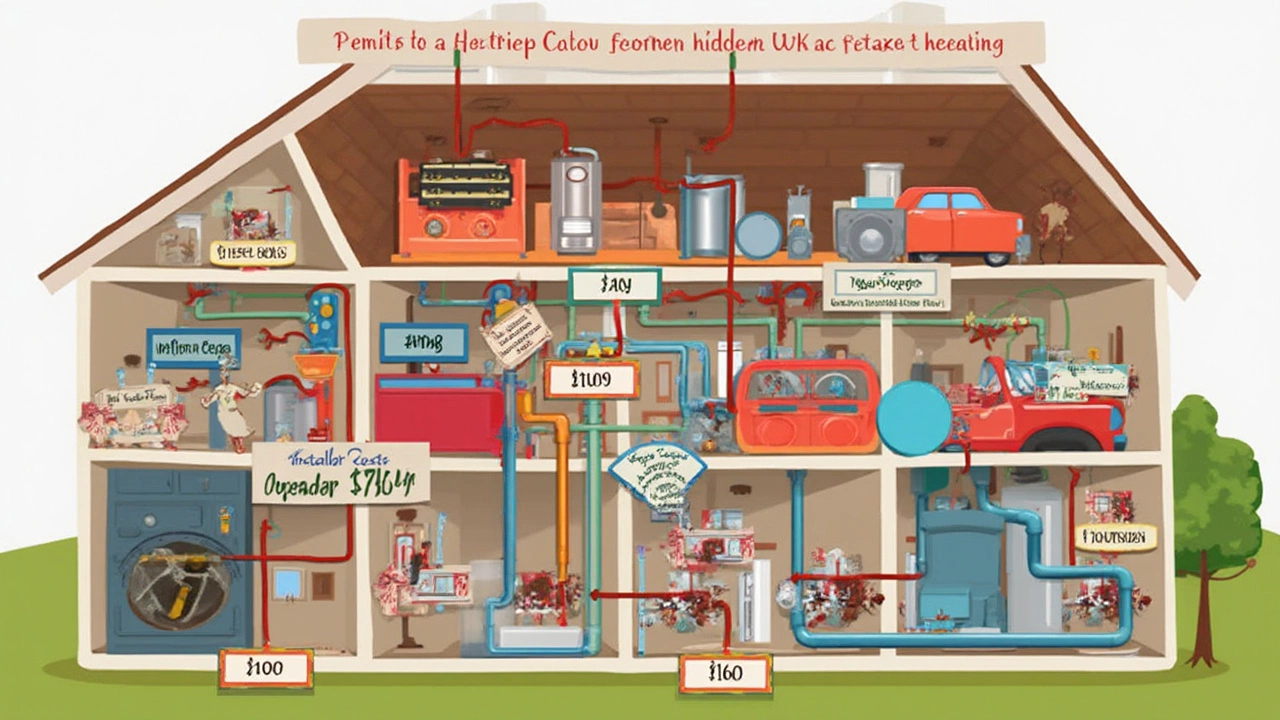
Parts, Pipework, and the Real Cost of Upgrades
Many people assume the boiler unit is the expensive bit, but hold on—a chunk of the cost disappears into hidden pipes, replacement valves, and alterations to old systems. In homes built before the 1980s, original plumbing may not meet today’s pressure or safety needs. Imagine your old copper pipes giving up the ghost under the higher pressures of a new condensing boiler. Suddenly, what started as a straight swap turns into a plumbing overhaul.
Every joint, pump, and fitting adds up. Modern boilers often need updated wall brackets, condensate pumps for safe water drainage, and enhanced insulation to keep things efficient. The minimum for most full-system swaps? Expect 20 to 30 meters of new pipework—sometimes tucked behind walls for hundreds of dollars in labour. Smart thermostats, zone valves for different parts of the house, and filtration kits can also land on your bill, all in the name of energy savings and longevity.
New Zealand’s patchy housing stock plays a part here. Take Dunedin's famous freezing winters and often-damp homes. Installers usually end up beefing up insulation around new pipe runs to stop heat loss, sometimes even running new pipes above ground to avoid cold walls. This isn’t overkill—it keeps your running costs down in the long term. But at the install stage, those added hours and materials push up the sticker price.
The Global Supply Chain and Boiler Prices
Remember the supply issues that made everyday things costlier during and after the pandemic? Boilers caught in that same logjam. Most leading brands are imported from the UK, Germany, or Italy. Shipping costs tripled in 2022 and 2023, and while things have calmed down a little, costs are still high compared to pre-pandemic days. That’s not just the machine itself but also replacement parts, electronics, and even specialized hand tools installers need to get the job done right.
Here’s a stat from a New Zealand importer in 2024: the average wholesale cost of a mid-range condensing boiler jumped 22% from 2021-2024. That’s before installer mark-up. Combine that with the Kiwi dollar’s notorious swings, and budgeting for a new boiler becomes a real nail-biter. Some people tried to save money by importing their own boilers, only to find the cost of transporting, clearing customs, and retrofitting to local standards wiped out any savings—and then some. Warranties often won’t apply if the unit’s not locally sourced, either.
It’s tempting to go with a no-name brand online, but a lot of Kiwi installers turn those jobs down. Bad experiences with spare parts, customer support, and software updates make many stick to proven names like Rinnai, Bosch, or Worcester. They simply last longer and perform better in New Zealand’s mixed climate. If you want a deal, the sweet spot is last year’s model—or finding a local wholesaler with factory seconds or ex-showroom stock with full warranties.

Tips for Saving on Your Next Boiler Replacement
So, is there any way to claw back some cash? There are a few tricks and negotiation tactics locals use in Dunedin—and they work elsewhere too. First, always get three quotes. Not just for price, but so you can compare recommendations: one installer may want to overhaul your system, while another suggests a much simpler fix. Ask if the new boiler is sized right for your home; too big, and you’re wasting money on both purchase price and running costs.
- Time your install for spring or late summer. Installer demand drops outside winter, and you’re more likely to score a deal or even same-week service.
- Ask about well-rated, slightly older stock. Installers often have last year’s models at a better price, with the same warranty and efficiency as the latest shiny release.
- Bundle the job—if you need a new hot water cylinder or radiator upgrade, some companies will cut you a deal if they get all the work in one shot.
- Don’t ignore rebates. In some regions, local councils sponsor ‘clean heat’ upgrades for old homes. These don’t always cover boilers, but it pays to check before you write the cheque.
- Maintain your new boiler. Book the annual service, keep an eye on pressure, and ask for installer support numbers in case anything goes off. A little TLC can hush up big, expensive repairs or premature replacement down the line.
The right questions save cash. Quiz your installer about all options, expected running costs, and how future upgrades work—like adding a heat pump or solar in a few years. If you’ve got mates who’ve swapped out their heating lately, hit them up for referrals. Word-of-mouth in places like Dunedin is still gold, especially when it comes to trades you can trust in your home.